Oil-water separator
【Product Introduction (DI-OS A Series)】
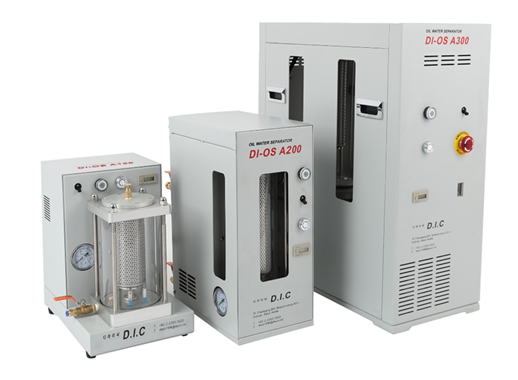
"DI-OS A Series" is a device that effectively removes moisture from vacuum pump oil, which causes malfunction of oil-type vacuum pumps, and improves the operating efficiency of facilities.
If vacuum pump oil contains moisture, the moisture attaches to the metal surface, causing the metal to rust, and by releasing the rust into the oil, it acts as a catalyst and accelerates the oxidation and deterioration of the oil.
Because of the presence of moisture, the oxidation rate of oil is accelerated tens or hundreds of times, making it much more harmful than ordinary sludge.
To solve this problem, we developed the DI-OS A Series, a device that separates moisture.
It effectively removes moisture in oil to maintain a stable operation rate of equipment.
How Rotary Vacuum Pumps Work and the Role of Vacuum Oil
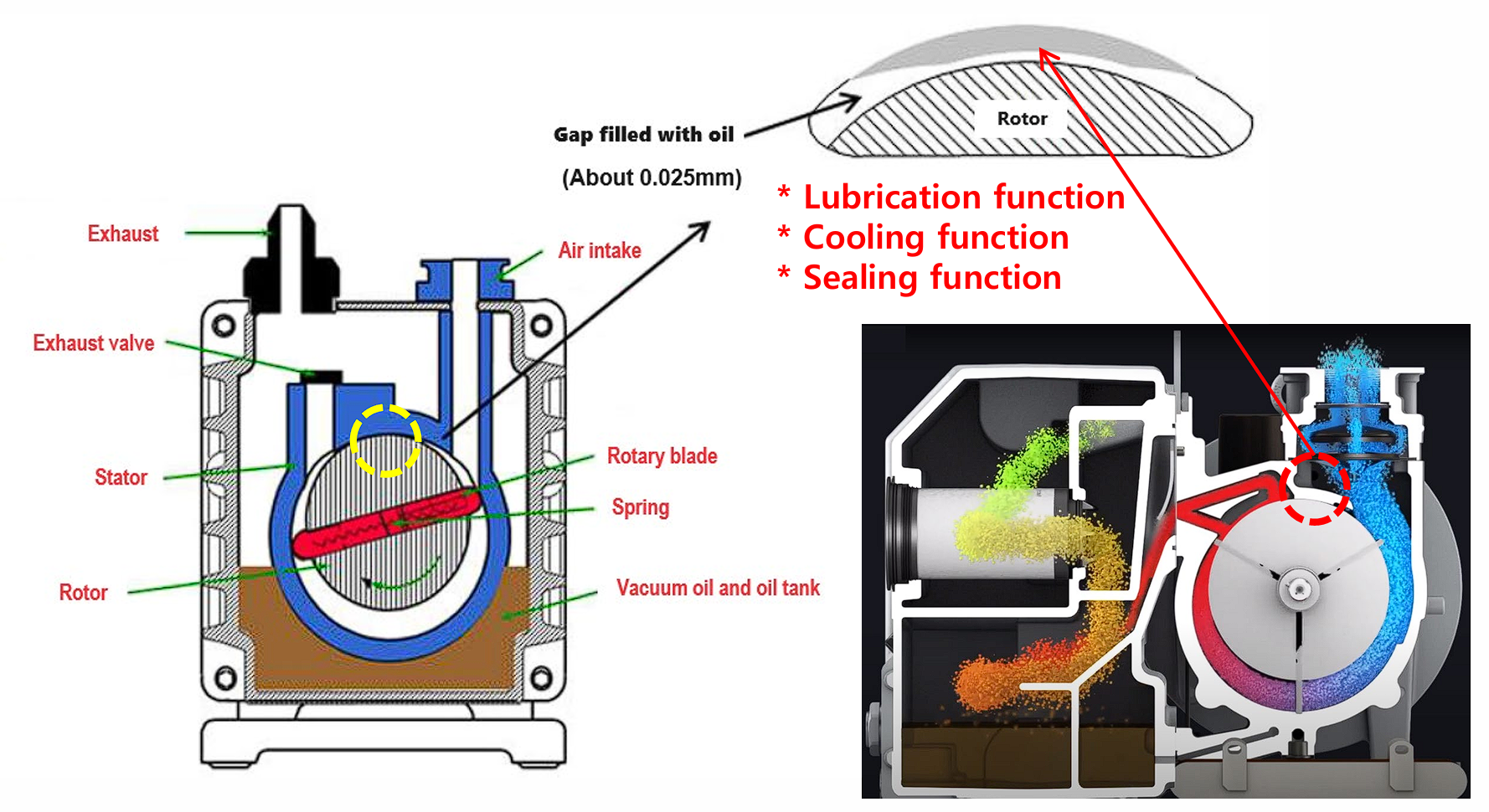
A rotary pump (Oil Sealed Rotary Vane Pump) creates a vacuum by discharging gas molecules in the chamber to the outside using oil-covered rotary blades.
The wings attached to the rotor rotating at high speed and the wall of the cylindrical chamber are assembled with a gap of about 0.025 mm, and oil is filled between them to lubricate, cool friction heat, and act as a seal to prevent gaps.
Oil circulates inside the pump from the oil reservoir and is discharged along with the compressed gas molecules through the discharge valve.
What happens when moisture gets mixed in the vacuum pump oil
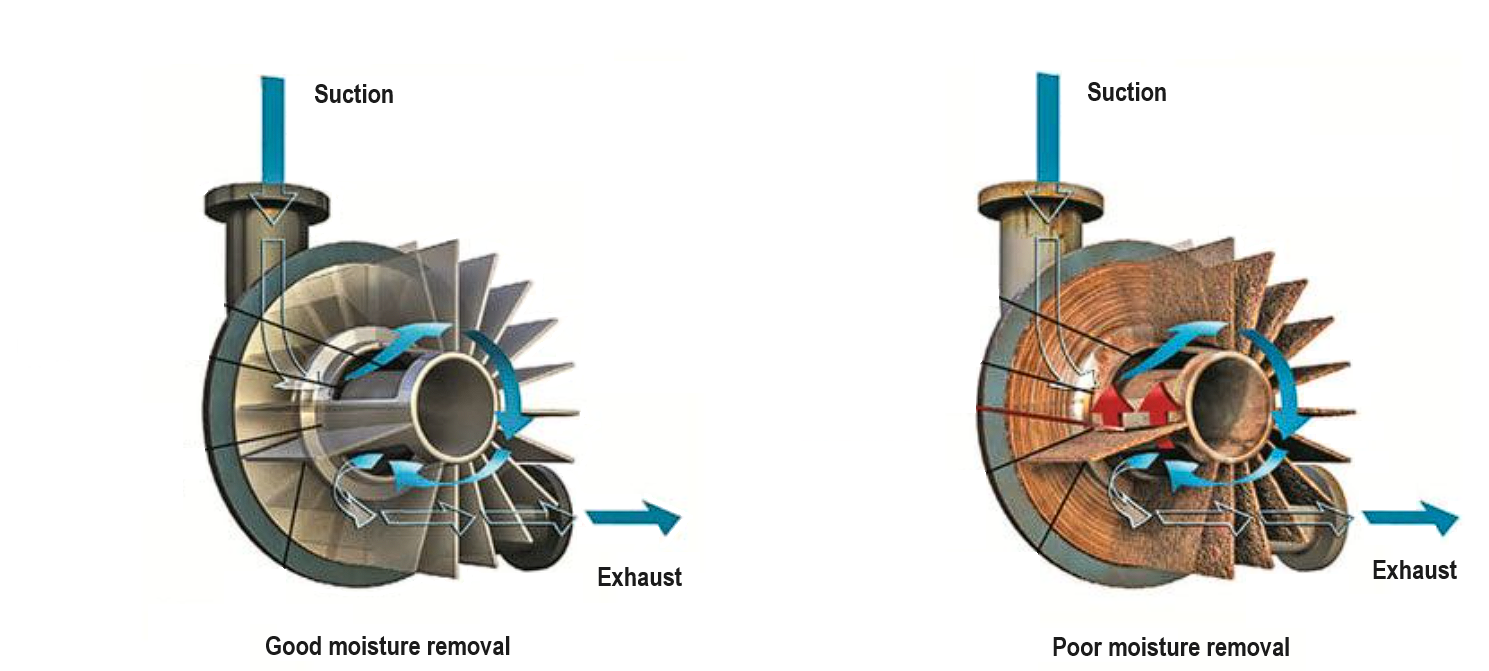
Moisture contained in the compressed gas molecules circulated by the vacuum pump mixes with oil during the suction and discharge process, causing the following fatal defects.
① Deterioration of lubrication and sealing function
– In the case of elastohydrodynamic (EHD) contact, which is the section with the smallest gap between the rotor blade and the chamber wall, the viscosity of the oil increases as the pressure increases, resulting in great strength in the lubricating film.
However, water (moisture) does not have these properties, so its viscosity remains constant or drops slightly as pressure increases.
As a result, the presence of moisture in the oil can increase the likelihood of contact between the rotor blades and the chamber, and in these high-pressure areas, hydrogen-induced wear, a complex friction chemical reaction, occurs, resulting in bubbles.
Hydrogen-induced wear is also expressed as hydrogen embrittlement. As a result of the high pressure generated in the pressurized area, water molecules are decomposed into their constituent oxygen and hydrogen atoms, and the hydrogen ions thus generated are absorbed into the surface of metal or non-metal, damaging the material. It weakens or makes it brittle, causing cracks.
In addition, lowered oil viscosity not only increases the possibility of friction between metals, but also reduces the sealing function, which can cause a backflow phenomenon in which compressed gas is sent to the intake stroke area without being effectively discharged.
② Occurrence of steam cavitation
– When the vapor pressure of water is reached in the low-pressure area of the chamber, steam bubbles are generated, and then in the high-pressure area, the water vapor bubbles quickly shrink (explode) and condense back into the liquid phase at the same time.
At this time, the water droplets form needle-shaped microjets and impact a small area of the metal surface with great force, causing localized surface fatigue and erosion.
③ Creation of corrosive by-products due to rust and corrosion
– Water directly attacks iron and steel surfaces, producing iron oxide, which combines with acids in oil to increase the corrosion potential of ferrous and non-ferrous metals.
Rust and corrosion generated in this way are easily separated from the surface and turn into a type of abrasive particle, accelerating rapid surface deterioration.
If the above phenomenon continues and is repeated, the contact gap becomes wider and vacuum efficiency rapidly decreases.
Therefore, efforts to remove moisture mixed in oil can be said to be the most basic and core element of all vacuum system management.
hydrogen embrittlement phenomenon
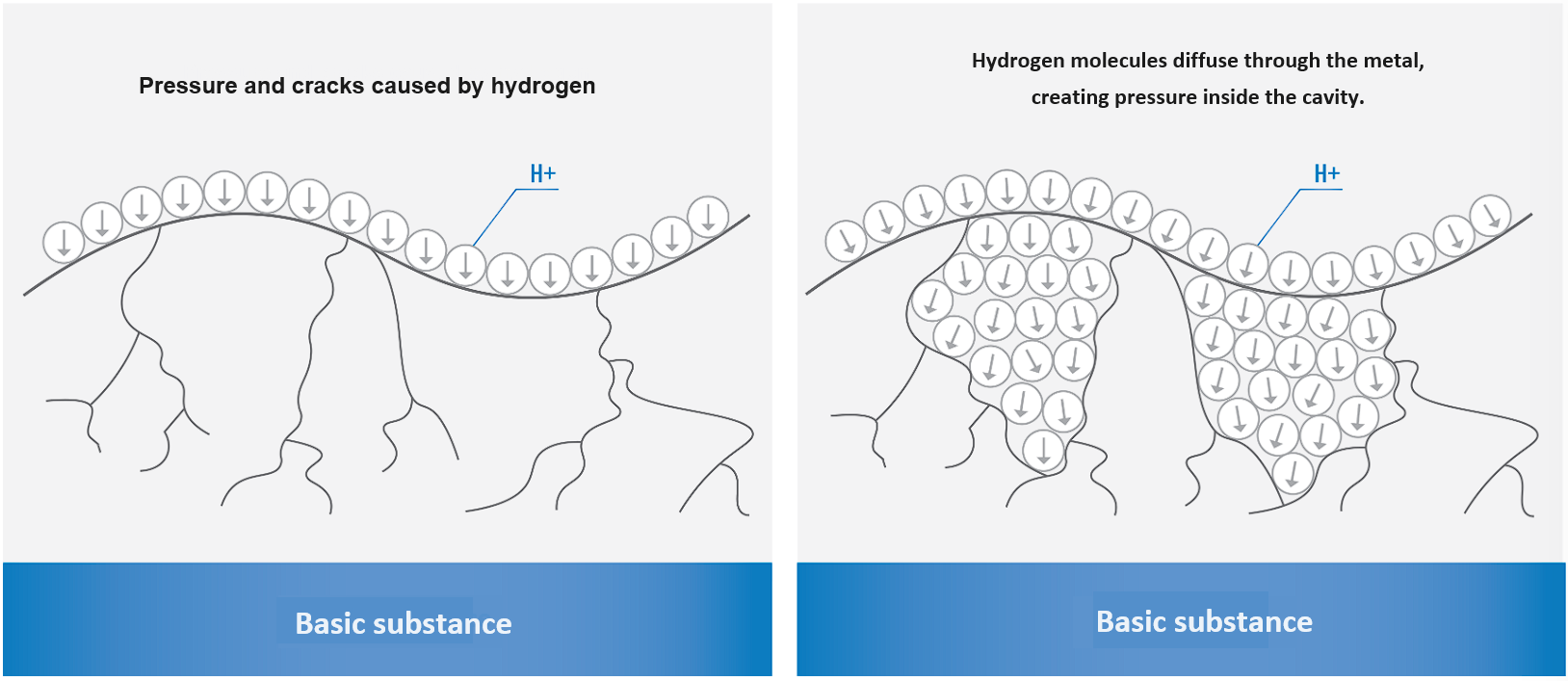
【Functions and specifications by model】
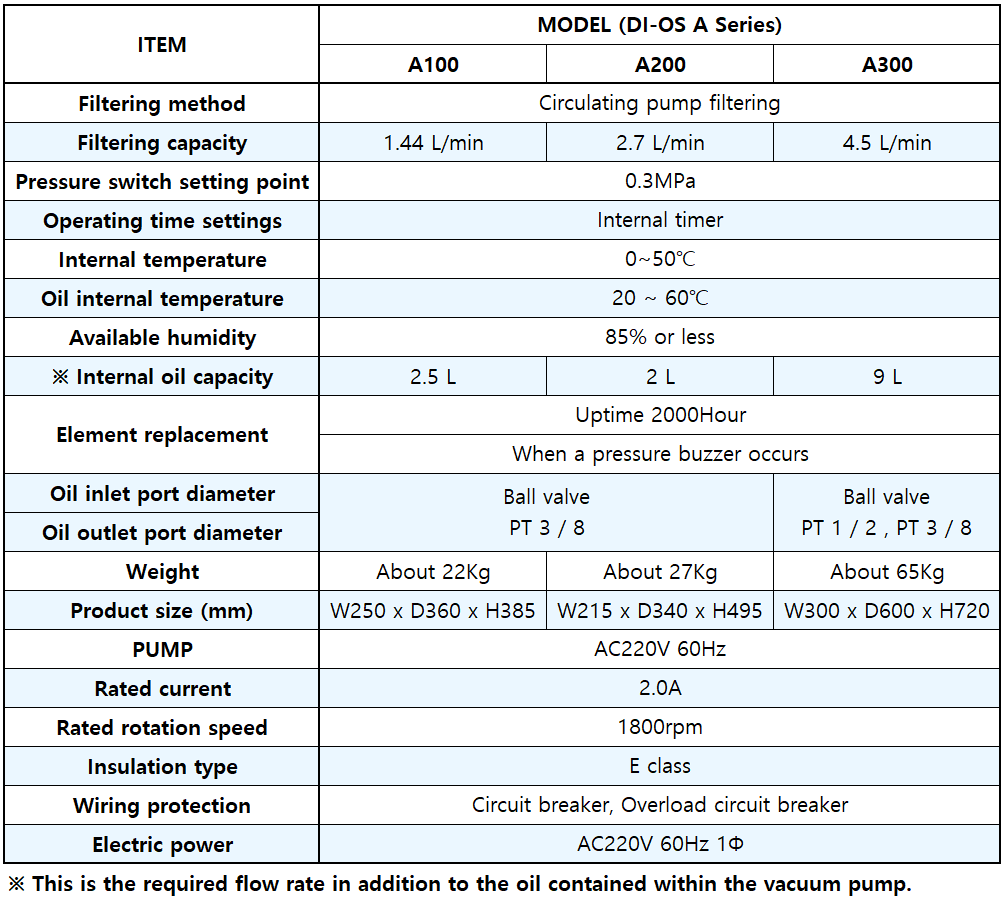
【Selection by model】

【System Construction】 ※ DI-OS A200 example
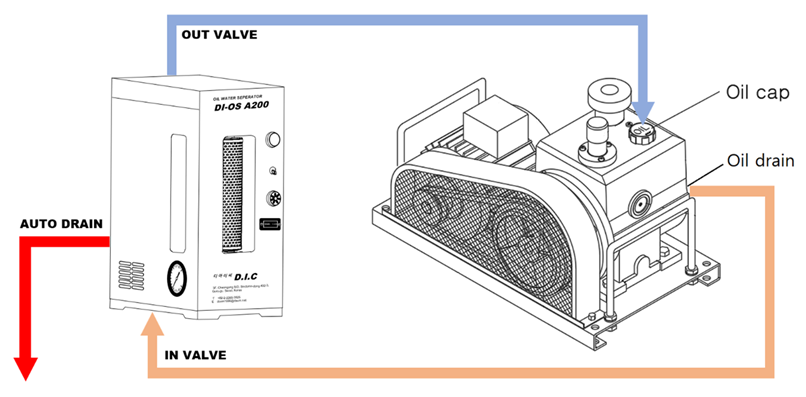
【System Functions and Connections】
1. Automatic discharge when a certain amount of moisture is collected
2. Check filter life time
3. Alarm occurs when operation is not possible due to filter blockage.
4. Electrical connection
> Always ON in standalone operation
> When interlocked with a vacuum pump, it automatically stops when the vacuum pump starts and after about 30 minutes (adjustment) of operation.
> Integration with an external PLC
【Filtering】
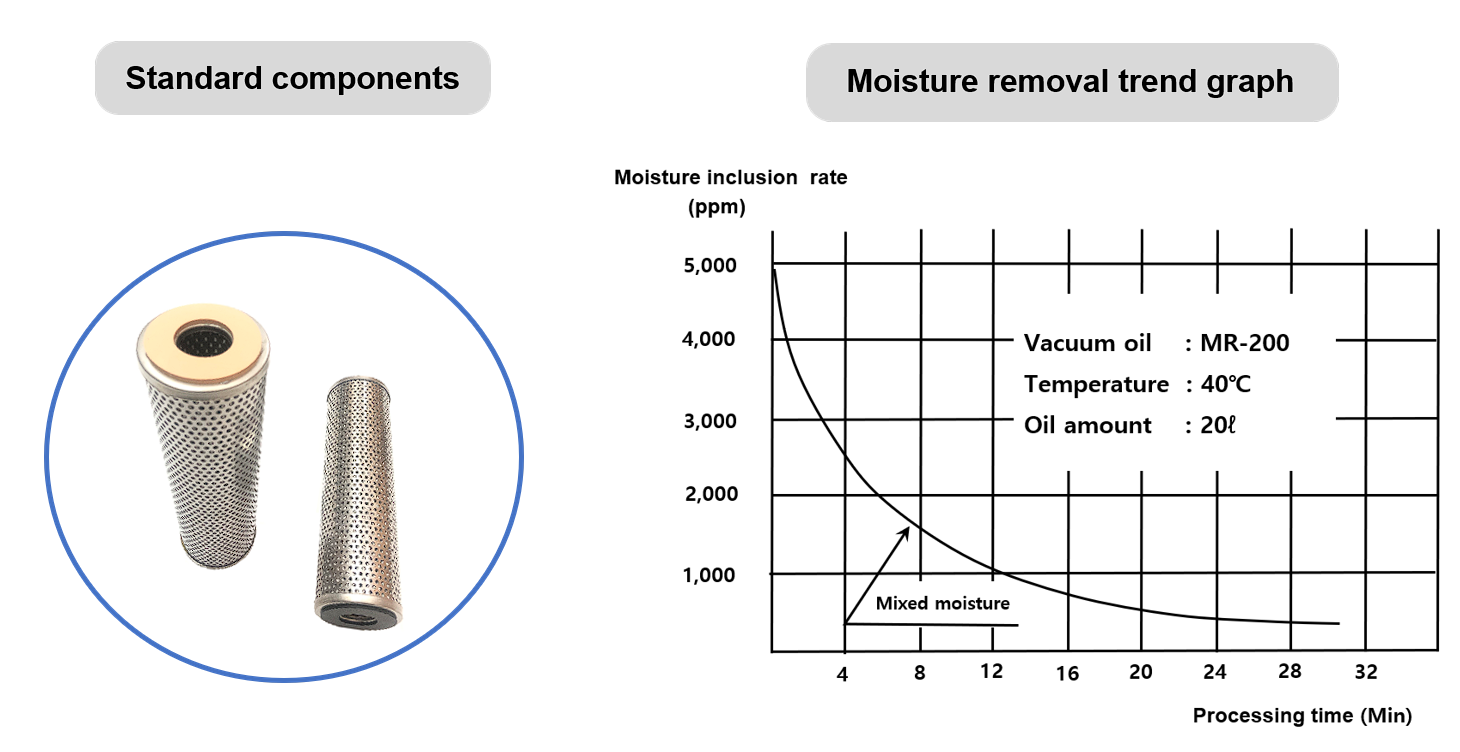
【Effect of application】
The flocculation element, using a special material, assembles the water, and the separation element forms a curtain of water to settle and separate the water.
The DI-OS A Series is a dehumidifier designed to reduce moisture values down to 200 ppm by applying it when the moisture level is above 2000 ppm (0.2%) or when moisture is always present.
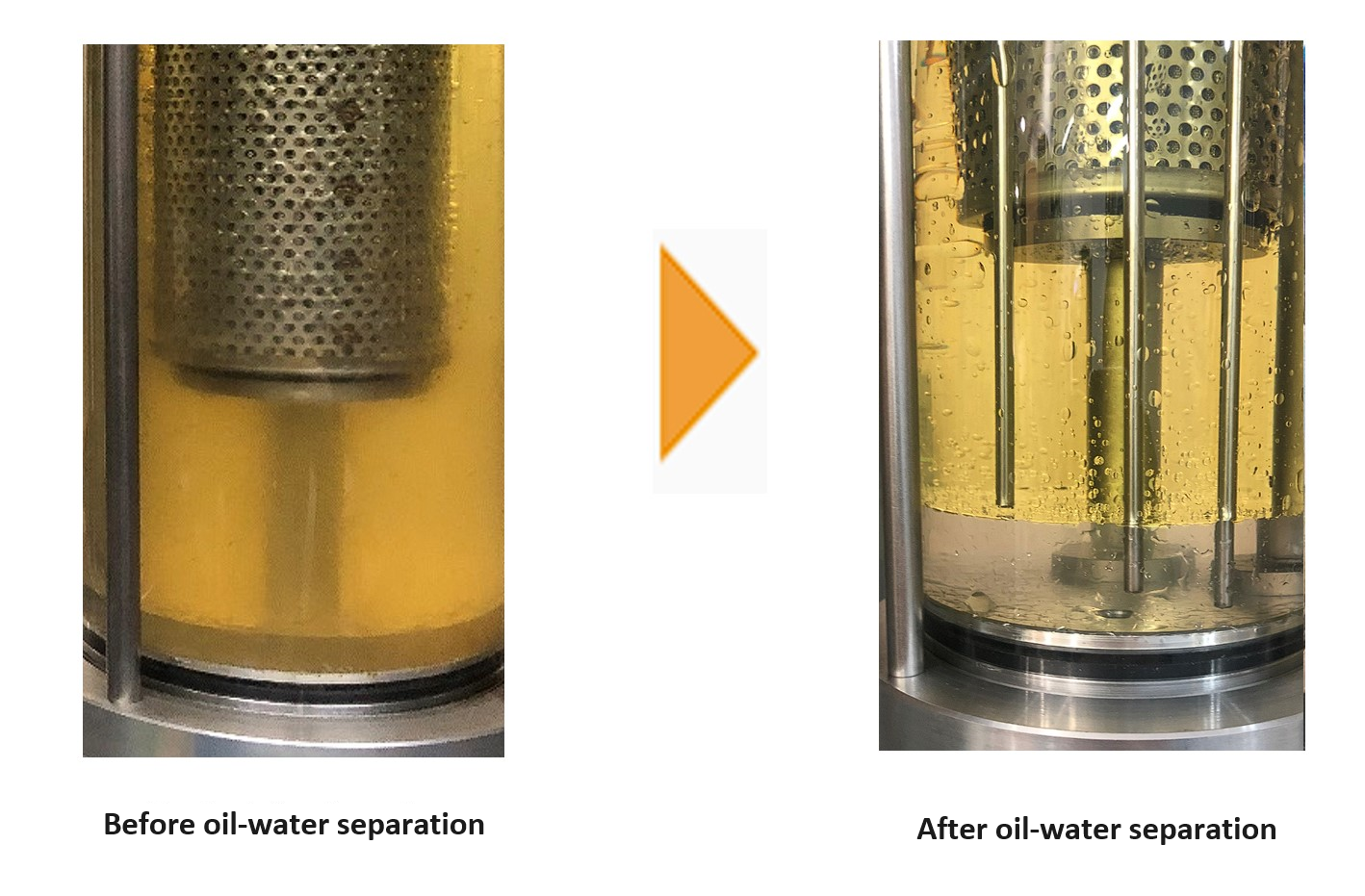
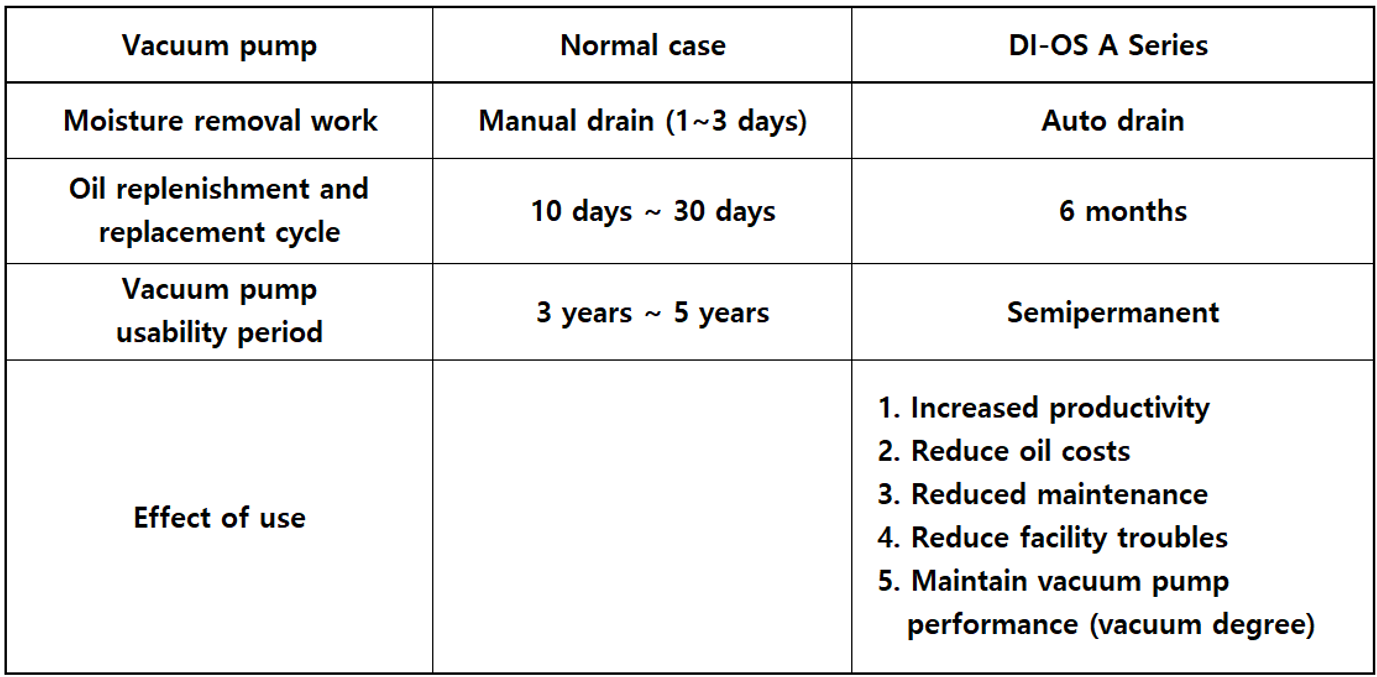
【Usage】
· Vacuum drying
· Vacuum deposition
· Vacuum brazing
· Distillation
· Vacuum packaging
· Vacuum freeze drying
· Vacuum heat treatment
· Vacuum impregnation
· Other vacuum devices and machines
The moisture that is constantly mixed in, even if it is only a small amount, turns into a large amount of moisture without us realizing it.
In this case, DI-OS A Series is the best choice.
【caution】
1. When the mixed moisture is acidic, the absorption ability decreases.
2. Models vary depending on the amount and type of moisture mixed in the oil. Please consult first.
3. Caution is required with acids and alkalis. Please provide information on the oil subject to disposal in advance.
【Automatic separation/ejection video】
【Installation example】
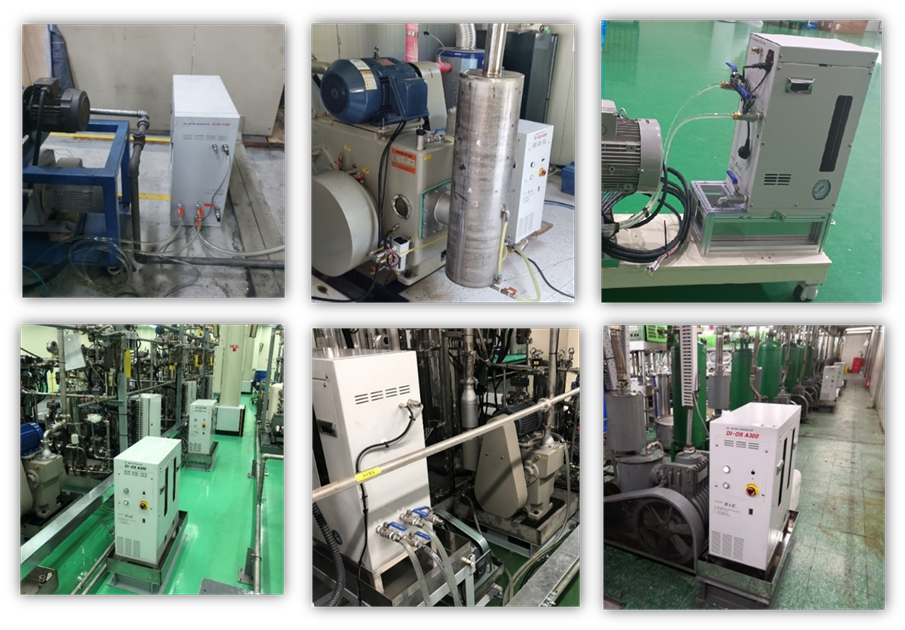